Deep offshore technology represents a fascinating intersection of engineering, environmental science, and resource management. This field pushes the boundaries of human innovation, allowing us to explore and exploit resources from the deepest parts of our oceans. From the design of sophisticated underwater robots to the implementation of robust safety protocols, deep offshore technology demands a high level of expertise and a commitment to responsible resource extraction and environmental stewardship. The challenges are immense, encompassing the logistical hurdles of operating in extreme environments and the imperative to minimize the environmental footprint of these operations.
This exploration delves into the various facets of deep offshore technology, examining the environmental impacts, technological advancements, logistical complexities, and economic considerations. We will also investigate the safety measures, legal frameworks, and the burgeoning field of deep offshore renewable energy, painting a comprehensive picture of this critical and evolving sector.
Deep Offshore Environmental Impact
The expansion of deep offshore resource extraction, encompassing both oil and gas extraction and deep-sea mining, presents significant ecological challenges. The unique and often fragile nature of deep-sea ecosystems makes them particularly vulnerable to the impacts of these activities, leading to potentially irreversible damage. Understanding these impacts is crucial for developing effective mitigation strategies and ensuring the long-term health of our oceans.
Ecological Consequences of Deep Offshore Oil and Gas Extraction
Deepwater oil spills, while less frequent than those in shallower waters, can have devastating and long-lasting consequences. The high pressure and low temperatures at these depths hinder the natural biodegradation processes, prolonging the exposure of marine life to toxic hydrocarbons. Furthermore, the disruption of the seabed during drilling and pipeline installation can damage benthic habitats, affecting a wide range of species, from corals and sponges to fish and invertebrates. The noise pollution generated by drilling operations can also disrupt the communication and navigation of marine mammals, potentially impacting their foraging and breeding behaviors. The Deepwater Horizon oil spill in the Gulf of Mexico serves as a stark reminder of the scale and severity of potential damage, with long-term effects still being observed on marine ecosystems and coastal communities.
Effects of Deep-Sea Mining on Marine Ecosystems
Deep-sea mining, targeting valuable minerals like polymetallic nodules, cobalt crusts, and seafloor massive sulfides, poses a significant threat to deep-sea ecosystems. The process involves disturbing vast areas of the seabed, destroying benthic habitats and releasing plumes of sediment that can smother filter-feeding organisms and reduce water clarity. These activities can also generate noise and light pollution, further impacting marine life. The potential for long-term biodiversity loss is substantial, given the slow growth rates and limited dispersal abilities of many deep-sea species. The lack of comprehensive understanding of deep-sea ecosystems makes predicting the full extent of the damage particularly challenging. For example, the mining of polymetallic nodules could significantly impact the unique biodiversity associated with these formations, including specialized species adapted to these specific environments.
Challenges in Monitoring and Mitigating Environmental Damage
Monitoring and mitigating environmental damage in deep offshore operations present significant technological and logistical challenges. The extreme depths, high pressures, and remoteness of these environments make access difficult and expensive. Developing effective monitoring technologies capable of detecting and quantifying the impacts of these activities in real-time is a major hurdle. Furthermore, the complexity of deep-sea ecosystems and the lack of baseline data make it difficult to assess the extent of damage and develop effective mitigation strategies. Establishing robust environmental regulations and enforcement mechanisms is crucial, along with the development of innovative technologies for environmental monitoring and remediation.
Comparison of Environmental Impacts of Deep Offshore Technologies
Technology | Habitat Destruction | Pollution (Water/Sediment) | Noise Pollution |
---|---|---|---|
Deepwater Oil & Gas Extraction | High (localized) | High (oil spills, drilling fluids) | High |
Deep-Sea Mining (Polymetallic Nodules) | Very High (extensive area) | High (sediment plumes, metals) | Moderate to High |
Deep-Sea Mining (Cobalt Crusts) | High (localized) | Moderate (metal release) | Moderate |
Deep-Sea Mining (Seafloor Massive Sulfides) | High (localized) | High (hydrothermal vent disruption, metals) | Moderate |
Technological Advancements in Deep Offshore Exploration
The push for deeper and more efficient offshore resource extraction has driven significant technological advancements in recent years. These advancements encompass improvements in underwater robotics, the integration of artificial intelligence, the development of advanced sensing and imaging technologies, and refinements in deep-sea drilling and well completion techniques. This section details some of the key innovations transforming deep offshore exploration.
Underwater Robotics for Deep Offshore Exploration
Recent advancements in underwater robotics have dramatically expanded our ability to explore and operate in the deep ocean. Autonomous Underwater Vehicles (AUVs) and Remotely Operated Vehicles (ROVs) are increasingly sophisticated, boasting enhanced maneuverability, longer operational endurance, and improved sensor capabilities. For instance, AUVs now utilize advanced navigation systems, including inertial navigation and acoustic positioning, allowing for precise mapping of the seabed and autonomous inspection of subsea infrastructure. ROVs, controlled remotely by operators on surface vessels, are equipped with high-definition cameras, manipulators for sample collection and intervention tasks, and various sensors for measuring water parameters, detecting hydrocarbon leaks, and assessing the condition of subsea structures. The development of hybrid AUV/ROV systems combines the advantages of both, offering increased flexibility and operational efficiency. These robotic platforms are critical for tasks ranging from geological surveys and pipeline inspections to the deployment and maintenance of subsea equipment.
The Role of Artificial Intelligence in Optimizing Deep Offshore Operations
Artificial intelligence (AI) is rapidly changing the landscape of deep offshore operations. AI algorithms are employed in various aspects, from optimizing drilling parameters and predicting equipment failures to analyzing seismic data and identifying potential hydrocarbon reservoirs. Machine learning models, trained on vast datasets of operational and geological information, can significantly improve the efficiency and safety of deep-sea drilling and production. For example, AI can analyze real-time data from sensors on drilling rigs to predict potential risks and prevent costly downtime. In subsea production, AI can optimize the operation of complex systems by adjusting parameters such as flow rates and pressure to maximize production while minimizing energy consumption. Furthermore, AI-powered image recognition systems are used to analyze underwater imagery and identify anomalies or potential hazards, improving the effectiveness of inspection and maintenance operations. The integration of AI is leading to more autonomous and intelligent deep-sea operations, reducing human intervention and improving overall performance.
Advanced Sensors and Imaging Techniques for Deep-Sea Exploration
The exploration of the deep ocean relies heavily on advanced sensors and imaging techniques. High-resolution multibeam sonar systems provide detailed maps of the seabed topography, revealing geological features crucial for identifying potential hydrocarbon reservoirs. Sub-bottom profilers use acoustic waves to penetrate the seafloor, revealing subsurface structures and geological layers. Advanced underwater cameras, equipped with high-resolution sensors and specialized lighting systems, capture detailed images of the seafloor and subsea structures. These cameras can be integrated into ROVs or AUVs for detailed inspections and surveys. Furthermore, hyperspectral imaging systems provide detailed spectral information about the seabed, allowing for the identification of various materials and geological features. These advanced sensing and imaging techniques provide crucial information for geological interpretation, reservoir characterization, and environmental monitoring.
Deep-Sea Drilling and Well Completion Methods
Deep-sea drilling and well completion present unique challenges due to the high pressures and temperatures encountered at great depths. Several methods are employed, each with its own advantages and disadvantages. One common method is the use of riser-based drilling, where a steel pipe extends from the surface to the seabed, providing a conduit for drilling fluids and protecting the wellbore. This method is generally more expensive but offers better control and safety compared to other methods. Alternatively, subsea drilling systems use remotely operated equipment on the seabed, reducing the need for a large surface vessel and potentially lowering costs. However, this method requires advanced robotics and control systems. Well completion techniques in deep water often involve the use of advanced wellhead equipment and subsea production systems, designed to withstand the harsh environment and maximize production efficiency. The choice of drilling and well completion method depends on several factors, including water depth, reservoir characteristics, and economic considerations. For instance, the use of advanced drilling fluids and specialized cementing techniques are essential to ensure well integrity and prevent environmental hazards.
Deep Offshore Infrastructure and Logistics
Deep offshore oil and gas extraction necessitates a complex and robust infrastructure, coupled with sophisticated logistical planning to overcome the inherent challenges of operating in such a remote and demanding environment. The scale and complexity of these operations require careful consideration of design, construction, maintenance, and transportation of personnel and equipment.
The logistical challenges are substantial, ranging from the sheer distance to the platform from shore to the harsh marine conditions encountered. Efficient and safe transportation of personnel, materials, and equipment is critical for the successful operation of deep offshore facilities. Specialized vessels and equipment play a pivotal role in mitigating these challenges, enabling efficient operations and ensuring safety.
Deep offshore technology necessitates robust solutions for data acquisition and remote operations. This often involves sophisticated systems relying on cutting-edge capabilities, such as those offered by advanced technology services , to ensure reliable performance in harsh environments. Ultimately, the success of deep offshore projects hinges on the seamless integration of these advanced services, enabling efficient and safe operations.
Deep Offshore Platform Infrastructure Schematic
Imagine a schematic diagram depicting a deep offshore oil platform. At the heart of the system is the platform itself, a large structure typically composed of steel or concrete, resting on the seabed or floating on the water’s surface. Submerged beneath the platform is a network of subsea pipelines and wellheads, connecting to the wells on the seabed. These pipelines transport hydrocarbons to the platform for processing. Above the waterline, the platform houses drilling equipment, processing facilities, living quarters for personnel, and helipads for transportation. A riser system connects the subsea infrastructure to the platform, allowing for the flow of fluids. Power generation is typically on-site, using gas turbines or other suitable power sources. Finally, a network of support vessels, including supply ships and maintenance vessels, operates around the platform, providing essential services.
Logistical Challenges of Deep Offshore Operations
Transporting equipment and personnel to remote deep offshore locations presents significant logistical hurdles. The sheer distance from shore requires specialized vessels capable of withstanding harsh sea conditions. These include Platform Supply Vessels (PSVs) and other specialized support vessels designed for long voyages and the transfer of heavy equipment. The weather also plays a crucial role; storms and rough seas can severely disrupt operations, leading to delays and potential safety risks. The remote location also limits the availability of support and emergency services, necessitating comprehensive safety protocols and contingency plans. The cost of transportation is also a significant factor, impacting the overall economics of deep offshore projects. For example, transporting a large drilling rig to a location 2000km offshore can take several days, with significant fuel costs and potential delays due to weather.
Specialized Vessels and Equipment
Deep offshore operations rely heavily on specialized vessels and equipment designed to withstand the challenging environment and perform specific tasks. Dynamic Positioning (DP) vessels, capable of maintaining precise position without anchors, are essential for various operations. These include drillships, floating production storage and offloading (FPSO) units, and subsea construction vessels. Remotely Operated Vehicles (ROVs) and Autonomous Underwater Vehicles (AUVs) are crucial for inspecting and maintaining subsea infrastructure, performing tasks that would be dangerous or impossible for human divers. Heavy-lift cranes and specialized lifting equipment are necessary for installing and removing heavy components on the platform and subsea. The use of these specialized vessels and equipment significantly reduces operational risks and improves efficiency, contributing to the overall success of deep offshore projects. For instance, the use of ROVs for subsea pipeline inspection significantly reduces the need for expensive and risky diver operations.
Deep offshore technology relies heavily on advanced semiconductor components for its complex systems. The performance of these systems, and thus the profitability of deep-sea operations, is indirectly tied to the success of companies like Micron, whose stock price you can check here: micron technology stock price. Therefore, fluctuations in the semiconductor market, as reflected in Micron’s stock, can have a ripple effect on the deep offshore industry’s technological advancements.
Maintenance and Repair of Deep Offshore Infrastructure
Maintaining and repairing deep offshore infrastructure is a complex and costly undertaking, requiring specialized skills and equipment. Regular inspections are crucial to identify potential problems early, using ROVs and other remote inspection technologies. Preventative maintenance strategies are employed to minimize the frequency and severity of repairs. Repair operations often involve specialized diving teams, ROVs, and support vessels equipped with the necessary tools and equipment. The use of advanced materials and construction techniques enhances the durability and longevity of the infrastructure. Remote diagnostics and predictive maintenance technologies are increasingly being used to optimize maintenance schedules and minimize downtime. A proactive approach to maintenance, coupled with advanced technologies, is crucial for ensuring the long-term safety and operational efficiency of deep offshore facilities. For example, regular inspection of riser systems using ROVs can detect corrosion or damage before it leads to a major incident.
Subsea Production Systems: Deep Offshore Technology
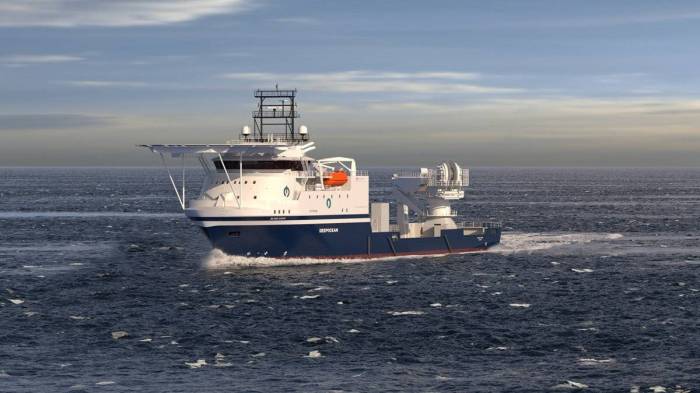
Subsea production systems represent a crucial element in maximizing the extraction of hydrocarbons from deepwater reservoirs. These complex systems enable the processing and transportation of oil and gas from the seabed to surface facilities, often located many kilometers away. Their design and implementation require advanced engineering, robust materials, and sophisticated control systems to withstand the harsh deep-ocean environment. This section details the components, functionality, and installation processes involved in these vital systems.
A typical subsea production system comprises several key components working in concert. These components are designed to withstand extreme pressure and corrosive environments. The system’s effectiveness depends on the seamless integration and reliable operation of each element.
Subsea Wellheads
Subsea wellheads are the interface between the producing reservoir and the subsea production system. They control the flow of hydrocarbons from the wellbore, providing pressure regulation and safety mechanisms. Several types exist, each suited to specific operational needs and well configurations. For instance, vertical, horizontal, and deviated wellheads cater to varying well trajectories, while different pressure ratings accommodate varying reservoir pressures. Tree types include, but are not limited to, standard, enhanced, and xmas trees. The choice depends on the specific well requirements and operational strategy.
Subsea Manifolds
Subsea manifolds are crucial for gathering hydrocarbons from multiple wells and directing them to the main export pipeline. They act as a central hub, allowing for efficient integration and management of production from various sources. They are typically constructed from robust materials to withstand the high pressures and harsh conditions of the deep ocean. The design incorporates multiple branches, each connected to an individual wellhead, with integrated flow control valves and pressure sensors. This facilitates flexible production management and optimized resource utilization.
Subsea Processing Equipment
Subsea processing equipment, including separators and pumps, allows for preliminary processing of the extracted hydrocarbons before export to the surface. This reduces the volume and improves the efficiency of transportation. Separators remove water and gas from the oil, increasing the oil’s value and reducing transportation costs. Pumps increase the pressure of the hydrocarbons, facilitating their efficient transport through pipelines over long distances. The inclusion of these processing units subsea minimizes the volume and complexity of the topside facilities.
Subsea Control Systems
Subsea control systems provide remote monitoring and control of the entire subsea production system. These systems use advanced sensors, actuators, and communication technologies to monitor production parameters, regulate flow rates, and manage safety systems. The data collected is transmitted to the surface facilities for real-time monitoring and intervention. Remote operation reduces risks associated with human intervention in hazardous subsea environments. The reliability of these systems is paramount for the safety and efficiency of the entire operation.
Subsea Oil and Gas Processing and Transportation
The process begins with the extraction of hydrocarbons from the reservoir through the wellhead. The hydrocarbons then flow through the subsea manifolds, where they are gathered and potentially undergo preliminary processing. Subsea separators separate the oil from gas and water, improving efficiency and reducing the transportation volume. Pumps then increase the pressure of the fluids for transportation through subsea pipelines to a floating production storage and offloading (FPSO) vessel or a fixed platform. The pipelines are typically made of high-strength steel and are carefully designed and laid to withstand the pressure and environmental conditions. The transported hydrocarbons are further processed on the surface facilities before being refined and marketed.
Installing and Commissioning a Subsea Production System
The installation and commissioning of a subsea production system is a complex and multi-stage process requiring precise planning and execution. The steps typically involve:
The installation and commissioning process requires meticulous planning and execution, and any deviation from the plan could result in significant delays and cost overruns.
- Detailed Engineering and Design: This phase includes the selection of appropriate equipment, design of the layout, and development of detailed installation plans.
- Fabrication and Testing: Subsea components are fabricated and rigorously tested to ensure they meet the required specifications and can withstand the harsh deep-ocean environment.
- Transportation and Mobilization: Specialized vessels transport the components to the installation site, where they are carefully mobilized and prepared for installation.
- Subsea Installation: Using remotely operated vehicles (ROVs) and other specialized equipment, the components are installed on the seabed and interconnected.
- Testing and Commissioning: The entire system is thoroughly tested to verify its functionality and ensure it operates as designed. This involves pressure testing, flow testing, and functional checks of all components.
- Start-up and Production: Once all tests are successfully completed, the system is started up and begins production of hydrocarbons.
Deepwater Risers and Flowlines
Deepwater risers and flowlines represent critical components in subsea oil and gas production, acting as the lifelines connecting subsea wells to surface facilities. Their design and maintenance are paramount for safe and efficient operations in the harsh deepwater environment. This section details the key considerations involved in their design, construction, and maintenance.
Deepwater Riser Design Considerations
The design of deepwater risers is heavily influenced by the challenging environmental conditions encountered at great depths. These include significant water depths, strong currents, high pressures, and the potential for extreme weather events such as hurricanes. Consequently, risers must be robust enough to withstand these forces while ensuring operational reliability and safety. Critical design parameters include material selection, structural integrity, fatigue resistance, and the ability to accommodate thermal expansion and contraction. For instance, the use of advanced materials and sophisticated analysis techniques, such as Finite Element Analysis (FEA), is crucial to predict and mitigate potential failure modes. Furthermore, the design often incorporates features to protect the riser from external damage, such as corrosion protection coatings and external insulation.
Deepwater Flowline Materials and Technologies
Deepwater flowlines, which transport hydrocarbons from subsea wells to processing facilities, are typically constructed from high-strength steel pipes. However, the choice of material and the construction techniques depend on several factors, including the fluid properties being transported, the environmental conditions, and the required lifespan. Advanced materials such as high-strength, low-alloy steels and corrosion-resistant alloys are often employed to enhance durability and longevity. In addition to material selection, the manufacturing process plays a significant role. Subsea flowlines are often manufactured using specialized welding techniques to ensure high-quality joints and minimize the risk of leaks. Furthermore, technologies such as flexible risers and pipelines are used in areas where the seabed is particularly uneven or where significant movement is anticipated. The use of sophisticated coating systems further protects the flowlines from corrosion and external damage.
Inspection and Maintenance of Deepwater Risers and Flowlines
Regular inspection and maintenance are vital for ensuring the integrity and operational reliability of deepwater risers and flowlines. These activities involve a combination of remote inspection techniques, such as remotely operated vehicles (ROVs) equipped with high-resolution cameras and sensors, and periodic in-situ inspection using specialized tools and divers. Non-destructive testing (NDT) methods, such as ultrasonic testing and magnetic particle inspection, are used to detect internal and external flaws. Maintenance activities may include repairs, replacements of damaged sections, and application of corrosion inhibitors. The frequency of inspection and maintenance is dictated by factors such as the age of the equipment, environmental conditions, and operational history. For instance, regular inspections might reveal signs of corrosion or fatigue, prompting necessary maintenance or replacement actions before catastrophic failure occurs. This proactive approach to maintenance significantly reduces the risk of operational disruptions and environmental damage.
Comparison of Riser and Flowline Materials
Several materials are used in the construction of deepwater risers and flowlines, each offering unique advantages and disadvantages. Steel remains the dominant material due to its high strength-to-weight ratio, weldability, and cost-effectiveness. However, steel is susceptible to corrosion, requiring protective coatings and regular inspection. Other materials, such as polymers and composite materials, are being explored for specialized applications. Polymers offer excellent corrosion resistance and flexibility, but their strength and temperature resistance may be limiting factors. Composite materials combine the strengths of different materials to achieve improved properties, but their cost and manufacturing complexity can be significant. The selection of the optimal material involves a trade-off between cost, performance, and environmental considerations. For example, while steel might be initially cheaper, the long-term costs associated with corrosion protection and potential repairs can outweigh the initial savings.
Remotely Operated Vehicles (ROVs) in Deep Offshore
Remotely Operated Vehicles (ROVs) are indispensable tools in modern deep offshore operations, extending human capabilities to inspect, maintain, and repair subsea infrastructure in environments inaccessible to divers. Their versatility and technological sophistication allow for a wide range of tasks, significantly improving efficiency and safety in the challenging deep-sea environment.
Modern ROVs are sophisticated robotic systems equipped with an array of sensors, manipulators, and tools that enable them to perform complex tasks remotely. They are controlled by skilled operators on surface vessels via a tether that provides power and communication. This tether, however, presents both advantages and limitations, as discussed below.
ROV Capabilities in Deep Offshore Operations
High-end ROVs possess remarkable capabilities. They are equipped with high-definition cameras providing real-time video feeds, allowing operators to visually assess the condition of subsea equipment. Advanced sonar systems enable the creation of detailed three-dimensional maps of the seabed and surrounding structures, crucial for navigation and identifying potential hazards. Manipulators, often equipped with interchangeable tools, provide the dexterity to perform delicate tasks such as manipulating valves, cutting cables, and connecting or disconnecting equipment. Specialized tools, such as water jets for cleaning, or cutting tools for removing debris, further expand their operational capacity. Some ROVs even carry sensors for measuring water chemistry, temperature, and pressure, providing vital environmental data.
ROV Use in Inspection, Maintenance, and Repair
ROVs play a crucial role in the inspection, maintenance, and repair (IMR) of subsea infrastructure. Regular inspections, facilitated by ROVs’ high-resolution cameras and sonar, allow for the early detection of corrosion, damage, or leaks in pipelines, risers, and other subsea equipment. This proactive approach minimizes the risk of costly repairs or environmental incidents. Maintenance tasks, such as cleaning debris from equipment or replacing components, can also be efficiently performed by ROVs using their manipulators and specialized tools. In the event of a failure, ROVs can conduct repairs, often avoiding the need for costly and time-consuming interventions using manned submersibles or diving operations. For example, an ROV can be deployed to quickly repair a small leak in a pipeline, preventing a larger environmental catastrophe.
Challenges of Operating ROVs in Extreme Deep-Sea Environments
Operating ROVs in extreme deep-sea environments presents several significant challenges. The immense pressure at these depths requires specialized pressure housings and materials capable of withstanding extreme forces. The lack of light necessitates powerful lighting systems for clear visibility. Strong currents and unpredictable weather conditions can impact the maneuverability and stability of the ROV, requiring sophisticated control systems and skilled operators. Communication delays caused by the long tether length can also affect the responsiveness of the ROV and hinder the operator’s ability to precisely control its movements. Furthermore, maintaining a reliable connection to the ROV over long distances is crucial, and any failure in the tether can lead to the loss of the vehicle. The extreme cold temperatures at these depths can also impact the functionality of electronic components, requiring robust and reliable equipment.
Key Features and Specifications of a High-End Deep-Sea ROV
The following points highlight the key features and specifications that characterize a high-end deep-sea ROV, showcasing their advanced capabilities and technological sophistication:
The design and capabilities of a high-end deep-sea ROV are a testament to the advancements in robotics and subsea technology. These specifications ensure optimal performance and reliability in the most challenging deep-ocean environments.
- Depth Rating: 6,000 meters (19,685 feet) or greater, enabling operation in the deepest parts of the ocean.
- Thrusters: Multiple high-power thrusters providing precise and powerful maneuverability in strong currents.
- Manipulators: Highly dexterous manipulators with interchangeable tools for a wide range of tasks.
- Cameras: High-definition cameras with multiple viewing angles and powerful lighting systems for clear visibility in low-light conditions.
- Sonar Systems: Advanced sonar systems for navigation, obstacle avoidance, and seabed mapping.
- Sensors: A suite of sensors for measuring water temperature, pressure, salinity, and other environmental parameters.
- Control System: A robust and reliable control system enabling precise and responsive operation from a surface vessel.
- Tether Management System: Sophisticated tether management system to prevent tangling and ensure reliable communication.
- Power System: High-capacity power system to support prolonged operation and the use of power-hungry tools and sensors.
- Pressure Housing: Robust pressure housing constructed from materials capable of withstanding extreme pressure at great depths.
Deep Offshore Safety and Risk Management
Deep offshore operations present a unique set of challenges due to the harsh and remote nature of the environment. The inherent risks associated with working at such depths necessitate robust safety protocols and a proactive approach to risk management. This section will Artikel the major hazards, regulatory frameworks, best practices, and emergency response procedures crucial for ensuring the safety of personnel and the protection of the environment.
Major Safety Hazards in Deep Offshore Operations
The deep offshore environment presents numerous hazards, many amplified by the remoteness and challenging conditions. These hazards span across various aspects of the operation, from the risks associated with the equipment itself to the potential for human error. Key hazards include: blowouts, equipment failure (including subsea wellheads, risers, and pipelines), fires and explosions, structural damage to platforms or vessels, severe weather events (hurricanes, cyclones), human error (fatigue, lack of training), and exposure to hazardous materials (oil spills, toxic gases). The consequences of incidents in these environments can be severe, with significant environmental and economic impacts alongside potential loss of life.
Safety Protocols and Regulations Governing Deep Offshore Activities
Stringent safety protocols and regulations govern deep offshore activities to mitigate the inherent risks. These regulations, often established by national and international bodies like the International Maritime Organization (IMO) and national regulatory authorities (e.g., the Bureau of Safety and Environmental Enforcement (BSEE) in the US), dictate design standards for offshore structures, operational procedures, emergency response plans, and personnel training. Compliance with these regulations is mandatory, and regular inspections and audits are conducted to ensure adherence. These regulations encompass aspects such as well control procedures, emergency shutdown systems, lifeboat drills, personal protective equipment (PPE) requirements, and environmental protection measures. For instance, detailed well control plans must be submitted and approved before any drilling commences, outlining procedures to prevent and mitigate blowouts.
Best Practices for Preventing Accidents and Minimizing Risks
Proactive risk management is paramount in deep offshore operations. Best practices encompass several key elements: rigorous risk assessments conducted throughout the project lifecycle, comprehensive training programs for all personnel, robust maintenance and inspection schedules for all equipment, implementation of advanced safety technologies (e.g., automated shutdown systems, real-time monitoring), and the fostering of a strong safety culture. Regular safety meetings, incident reporting systems, and near-miss reporting are crucial for identifying potential hazards and implementing corrective actions. Furthermore, the utilization of advanced simulation and training tools helps personnel prepare for various scenarios, enhancing their response capabilities during emergencies. Emphasis on human factors, including fatigue management and stress reduction strategies, is also essential for minimizing human error.
Emergency Response Procedures for a Deep Offshore Incident
The flowchart above illustrates a simplified emergency response procedure. A real-world scenario would involve far more complex steps and considerations, tailored to the specific nature of the incident and the offshore facility. The key is a well-rehearsed and clearly defined plan accessible to all personnel. Effective communication is critical, utilizing various channels (satellite phones, VHF radio, etc.) to ensure rapid dissemination of information and coordination of response teams. Regular drills and simulations are crucial for ensuring preparedness and effective execution of the plan.
Economic Aspects of Deep Offshore Technology
Deep offshore resource extraction presents a complex interplay of significant economic benefits and substantial challenges. The high capital expenditures, operational complexities, and inherent risks associated with this sector necessitate a thorough understanding of the financial landscape to assess its overall viability and impact. This section will explore the key economic drivers and constraints influencing deep offshore operations.
Economic Benefits of Deep Offshore Resource Extraction
The primary economic benefit stems from the access to vast reserves of oil and gas previously unreachable with conventional technologies. These resources contribute significantly to national energy security and revenue generation for both governments and private companies. The development of deep offshore fields creates employment opportunities across various sectors, including engineering, manufacturing, construction, and logistics, stimulating economic growth in related industries and regions. Furthermore, technological advancements spurred by deep offshore exploration often lead to innovations with broader applications across various industries, further boosting economic output. For example, the development of advanced subsea robotics has applications in underwater construction, marine research, and even search and rescue operations.
Cost Factors in Deep Offshore Infrastructure Development and Operation
Developing and operating deep offshore infrastructure demands substantial capital investment. The costs are significantly higher compared to onshore or shallow-water projects, primarily due to the specialized equipment, complex engineering designs, and challenging environmental conditions. These costs encompass exploration and appraisal activities, platform construction and installation, subsea pipeline construction, and ongoing maintenance and operational expenses. For instance, the construction of a single deepwater floating production, storage, and offloading (FPSO) unit can easily cost several billion dollars, reflecting the high capital intensity of deepwater projects. Furthermore, the remoteness of these locations necessitates significant investment in logistics and support infrastructure, adding to the overall project costs.
Impact of Fluctuating Energy Prices on Deep Offshore Investment Decisions
The profitability of deep offshore projects is highly sensitive to fluctuations in energy prices. High oil and gas prices generally incentivize investment in these expensive ventures, as the potential returns justify the high upfront costs and risks. Conversely, periods of low energy prices can render many deep offshore projects economically unviable, leading to project delays, cancellations, or even bankruptcies. The 2014 oil price crash, for example, significantly impacted deepwater project development globally, resulting in numerous project delays and cancellations. Investment decisions are therefore heavily influenced by price forecasts and risk assessments, with investors often demanding higher returns to compensate for the inherent volatility of the energy market.
Economic Viability of Deep Offshore Oil and Gas Extraction Compared to Other Energy Sources
The economic viability of deep offshore oil and gas extraction is constantly being reevaluated against the backdrop of competing energy sources, such as renewables (solar, wind, hydro) and nuclear power. While deep offshore resources remain a crucial part of the global energy mix, particularly in regions with significant reserves, the increasing competitiveness of renewable energy sources, driven by technological advancements and government subsidies, poses a challenge. The long lead times, high capital costs, and environmental concerns associated with deep offshore projects need to be carefully weighed against the lower costs and reduced environmental impact of some renewable energy alternatives. The ongoing transition to a lower-carbon energy system is likely to influence future investment decisions in deep offshore oil and gas extraction, with a greater emphasis on projects with lower carbon footprints and improved environmental performance.
Deep Offshore Renewable Energy Technologies
The vast expanse of the deep ocean, previously considered only for oil and gas extraction, now presents a significant opportunity for harnessing renewable energy resources. Technological advancements are making it increasingly feasible to tap into the immense potential of deep offshore wind and wave energy, offering a cleaner and more sustainable energy future. This section explores the various technologies involved, their potential, challenges, and economic viability.
Deep Offshore Wind Farms
Deep offshore wind farms utilize wind turbines located further from the coast in deeper waters, where wind speeds are generally higher and more consistent than in shallower areas. These farms typically employ larger, more powerful turbines mounted on floating platforms, such as spar buoys, tension leg platforms (TLPs), or semi-submersible structures, to withstand the harsh marine environment. The electricity generated is then transmitted to the shore via subsea cables. The higher wind speeds translate to increased energy generation compared to onshore or near-shore wind farms. For example, the Hywind Scotland project, featuring five floating wind turbines, demonstrated the viability of this technology, generating significant amounts of clean energy.
Wave Energy Converters
Wave energy converters (WECs) capture the kinetic energy of ocean waves and convert it into electricity. Several types of WECs exist, each with its own design and operating principles. These include oscillating water columns, point absorbers, overtopping devices, and wave energy farms. Deep ocean waves often possess greater energy density than those closer to shore, making deep-water locations attractive for large-scale wave energy projects. However, the challenging conditions of the deep ocean, including strong currents and extreme weather events, pose significant engineering challenges. The development of robust and efficient WECs capable of operating reliably in these environments is crucial for the successful deployment of wave energy farms.
Challenges and Opportunities in Deep Offshore Renewable Energy
Developing deep offshore renewable energy projects presents unique challenges. The remoteness of these locations increases the cost of installation and maintenance, requiring specialized vessels and equipment. The harsh marine environment demands robust and durable infrastructure capable of withstanding extreme weather conditions and corrosion. Furthermore, the transmission of electricity from the offshore site to the onshore grid requires long subsea cables, adding to the project’s complexity and cost. However, the potential benefits are significant. Deep offshore renewable energy offers a virtually inexhaustible supply of clean energy, helping to reduce reliance on fossil fuels and mitigate climate change. Technological innovation, government support, and private investment are crucial to overcoming the challenges and unlocking the full potential of this emerging energy sector.
Comparison of Deep Offshore Renewable Energy Technologies
Technology | Power Output (MW) | Installation Depth (m) | Estimated Cost ($/MW) | Economic Feasibility |
---|---|---|---|---|
Floating Offshore Wind Turbine | 8-15+ | 50-300+ | 4000-8000+ | High potential, but currently high CAPEX |
Wave Energy Converter (Point Absorber) | 0.5-5 | 20-100+ | 6000-15000+ | Significant technological advancements needed to reach grid parity |
Wave Energy Converter (Oscillating Water Column) | 1-10 | 10-50+ | 5000-12000+ | Moderate potential, cost reduction is key |
Tidal Energy Converter | 1-10+ | Variable (depends on location) | 5000-10000+ | High potential in suitable locations, but geographically limited |
Legal and Regulatory Frameworks for Deep Offshore Operations
The development and operation of deep offshore projects are subject to a complex web of international and national laws and regulations designed to protect the environment, ensure worker safety, and prevent accidents. These frameworks vary considerably depending on the geographical location, the type of activity (exploration, production, renewable energy), and the specific risks involved. Navigating this regulatory landscape is crucial for successful project execution.
Effective legal and regulatory frameworks are essential for mitigating the potential environmental and safety risks associated with deep offshore activities. They provide a structured approach to managing these risks, fostering responsible development while enabling the exploitation of valuable resources.
Key International and National Regulations Governing Deep Offshore Activities
International maritime law, as codified in the United Nations Convention on the Law of the Sea (UNCLOS), forms the foundation for many national deep offshore regulations. UNCLOS establishes the rights and responsibilities of coastal states over their continental shelves and exclusive economic zones, including the regulation of activities like exploration and exploitation of resources. Beyond UNCLOS, several international organizations, such as the International Maritime Organization (IMO) and the International Association of Drilling Contractors (IADC), issue guidelines and standards that significantly influence national regulations. Specific national laws vary widely; for example, the United States utilizes the Outer Continental Shelf Lands Act, while the UK relies on legislation such as the Offshore Petroleum Act. These national laws often incorporate international best practices and standards while addressing specific national contexts and concerns.
The Role of Environmental Impact Assessments in Deep Offshore Project Approvals, Deep offshore technology
Environmental Impact Assessments (EIAs) are critical components of the permitting process for deep offshore projects. EIAs are comprehensive studies evaluating the potential environmental consequences of a proposed project, considering factors such as marine life disruption, habitat destruction, and potential pollution from spills or discharges. These assessments must identify potential impacts, propose mitigation measures, and assess the overall environmental acceptability of the project. Regulatory bodies review EIAs rigorously, often requiring further studies or modifications before granting approval. For instance, a proposed deep-sea mining operation would require an extensive EIA addressing the potential impact on benthic communities and the wider marine ecosystem. The thoroughness and credibility of the EIA are paramount in gaining regulatory approval.
Mechanisms for Enforcing Safety and Environmental Regulations in Deep Offshore Operations
Enforcement of safety and environmental regulations in deep offshore operations typically involves a combination of proactive measures and reactive responses. Proactive measures include regular inspections by regulatory bodies, audits of safety and environmental management systems, and the certification of equipment and personnel. Reactive responses involve investigations into incidents and accidents, potential penalties for non-compliance, and the implementation of corrective actions. Stringent penalties, including fines and operational shutdowns, are imposed for serious violations. Regulatory bodies often collaborate with industry stakeholders to develop and implement effective enforcement mechanisms, fostering a culture of safety and environmental responsibility. For example, the consequences of a major oil spill can include substantial fines, legal action, and reputational damage, significantly impacting the responsible company.
The Process of Obtaining Permits and Licenses for Deep Offshore Projects
Securing the necessary permits and licenses for deep offshore projects is a complex and time-consuming process. It generally involves multiple stages, beginning with initial consultations with regulatory authorities, followed by the submission of comprehensive applications including detailed project plans, EIAs, and safety assessments. Applications undergo rigorous review, often involving public consultations and stakeholder engagement. Once approved, permits and licenses are issued, outlining specific conditions and requirements that must be met throughout the project lifecycle. The duration of the permitting process varies considerably depending on the project’s scale, complexity, and the regulatory environment. Failure to comply with permit conditions can lead to penalties or even project suspension. The entire process emphasizes transparency and accountability, aiming to balance economic development with environmental protection and public safety.
Closing Notes
In conclusion, deep offshore technology presents both immense opportunities and significant challenges. While the potential for resource extraction and renewable energy generation is substantial, responsible development is paramount. Balancing economic gains with environmental protection and robust safety measures requires a collaborative effort from industry, governments, and researchers. Continued innovation and a commitment to sustainable practices will be crucial in shaping the future of deep offshore operations and ensuring the long-term health of our oceans.